Sélectionnez individuellement des articles dans le tableau suivant pour obtenir des détails ainsi que des images et des documents supplémentaires.
Résine adhésive et liquide bicomposant CERAfix® 203
Résine liquide et adhésive bicomposant à base d'époxy pour le remplissage des fissures et des joints dans les chapes en ciment et le béton.
Inscrivez-vous dès maintenant pour accéder à plus de 125 000 produits !

Modèle(s) disponible(s)
Sac à trois chambres
- Application très propre, gant et supports de chape inclus
- Sacs à compartiments selon les besoins pour une distribution simple et rapide
- Mélange facile dans le sac, sans besoin d'outils
Excellentes propriétés de dispersion et de pénétration
- Pénètre dans les fissures les plus fines
- Extrêmement facile à utiliser
Hautement adhésif
- Crée des raccords solides et durables
- Excellente adhérence sur les surfaces minérales
Durcissement rapide
- Réduit les temps d'immobilisation
- Les travaux suivants peuvent être effectués rapidement
Résiste aux produits chimiques
Applications polyvalentes, notamment pour les zones soumises à des contraintes élevées, comme l'artisanat et l'industrie.
Résiste à l'eau et au gel après durcissement
Adapté aux systèmes de chauffage au sol et aux nattes chauffantes électriques
Ne pas sceller les fissures et les joints aveugles tant que la surface n'est pas prête à être couverte. Les températures élevées raccourcissent les temps d'application et de durcissement (se référer aux données techniques). Attention : le matériau restant dans le sac est chaud !
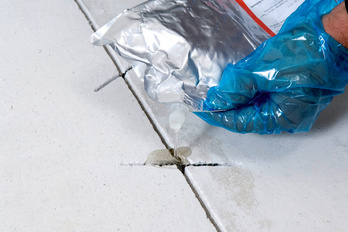
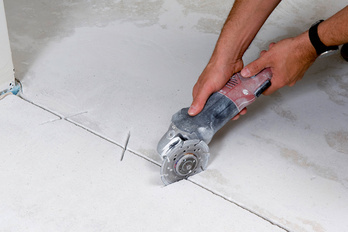
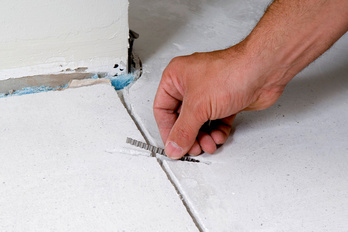
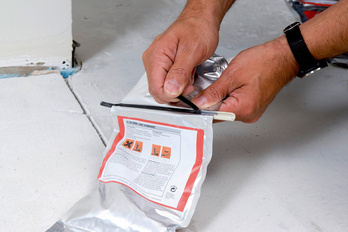
Le CERAfix 203 est principalement utilisé pour réaliser les chapes avec cavités et pour réaliser le scellement positif des fissures et des joints dans les chapes et dans le béton.
En outre, il est adapté comme résine de primaire, pour réparer les éclats de pierre et de béton, etc., lorsque des quantités de réaction avec la résine mineures sont requises. Il est recommandé d'utiliser le CERAfix 103 pour travailler sur de grandes surfaces.
Le CERAfix 203 est adapté aux chapes chaudes, pour une utilisation intérieure et extérieure ainsi qu'aux environnements exposés à l'humidité.
Le contenu du sac est mélangé comme suit pour toutes les applications :
Utiliser des équipements de protection individuelle (lunettes/masques, gants) ! Le durcisseur est acide ! Ouvrir le troisième compartiment sans endommager le premier et le deuxième. Retirer les gants jetables et les supports de chape. Retirer le cordon rond de la barrette de fixation et l'extraire du sac, de sorte que le contenu du premier et du deuxième compartiments du sac puisse être mélangé. Mélanger soigneusement les deux composants pendant environ 3 minutes en les malaxant et en les émulsionnant. Le matériau prêt à l'emploi doit être mélangé uniformément, de sorte à ne laisser aucune trace. Veiller à ne pas endommager le sac pendant l'opération de mélange. Mettre les gants de protection. Ouvrir le bouchon, si nécessaire rajouter un flexible en plastique. Ensuite, faire sortir le mélange en appuyant sur le conteneur et l'appliquer immédiatement.
1. Scellement des cavités :
- Percer ou exposer la cavité. L'air doit pouvoir s'échapper de la cavité ; par conséquent, percer un second trou de ventilation
- Ensuite, nettoyer et dépoussiérer soigneusement la zone
- Puis verser la résine liquide dans la cavité, en procédant par petites portions. Un coulage peut être nécessaire par la suite. Besoin en matériau : 1,1 kg/l volume
2. Scellement des fissures :
- Ouvrir la fissure et couper perpendiculairement par rapport à la fissure à une distance de 15 à 20 cm ; utiliser un disque à tronçonner adapté pour couper l'épaisseur de la chape sur une profondeur de 1/2 à 2/3. Les fentes transversales doivent être positionnées de manière centrale par rapport à la fissure et mesurer environ 10 cm de long
- Ensuite, nettoyer et dépoussiérer soigneusement la zone. Il est recommandé d'aspirer soigneusement toute la poussière dans la zone en utilisant un aspirateur industriel adapté
- Verser ensuite la résine mélangée dans la fissure et les joints par portions jusqu'à ce qu'ils soient visiblement saturés. Pour rallonger le bec verseur, il est possible de rajouter un flexible en plastique sur le conteneur
- Ensuite, insérer les supports de chape dans la fente transversale et étaler la résine émergente uniformément sur la surface
- Après environ 30 à 45 minutes, épandre du sable siliceux propre avec un calibre de grain de 0,2 à 1,0 mm au-dessus de la résine
- Après durcissement, nettoyer la surface et éliminer l'excédent de sable
3. Apprêtage :
- Préparer et nettoyer la surface conformément à ses spécifications
- Verser la résine mélangée sur la surface et l'étaler uniformément jusqu'à ce que la surface soit visiblement saturée
- Après environ 30 à 45 minutes, épandre du sable siliceux propre avec un calibre de grain de 0,2 à 1,0 mm au-dessus de la résine
- Après durcissement, nettoyer la surface et éliminer l'excédent de sable
4. Réparation des zones endommagées :
- Préparer et nettoyer la surface conformément à ses spécifications
- Ensuite, enduire la zone de primaire
- Un mortier est préparé pour réparer les zones fissurées et endommagées : Pour réparer les fissures plus profondes, il est possible de produire un mortier à base d'agent liant CERAfix 203 comme suit : Tout d'abord, ajouter du sable siliceux dans le seau de mélange puis verser la résine mélangée. 1 partie CERAfix 203 pour 7 à 10 parties de sable siliceux. Mélanger jusqu'à obtenir un composant uniforme. Le calibrage de grain du sable siliceux dépend de l'épaisseur de la couche à appliquer. L'épaisseur de couche minimum équivaut à environ trois fois le calibrage du plus gros grain. L'épaisseur de couche maximum équivaut à environ dix fois le calibrage du plus gros grain. Par exemple : Le sable siliceux utilisé possède un calibrage de grain compris entre 0 et 2 mm de diamètre. Par conséquent, il est possible de préparer un mortier pouvant être appliqué en couches d'environ 6 à 20 mm d'épaisseur.
- Appliquer et lisser le mortier mélangé sur la surface fraîchement apprêtée. Ensuite, épandre immédiatement du sable siliceux avec un calibre de grain de 0,2–1,0 mm sur le mortier venant d'être posé. Requis : environ 2,0 kg de mortier pour 1 m² et pour une épaisseur de couche de 1 mm.
5. Mastics de comblement des fissures :
- Préparer et nettoyer la surface conformément à ses spécifications
- Ensuite, enduire la zone de primaire
- Préparer du mortier pour combler les fissures comme suit : Tout d'abord, ajouter le sable siliceux avec un calibrage de grain de 0,2-1,0 mm dans le seau de mélange puis verser la résine. 1 partie CERAfix 203 pour 1 à 2 parties de sable siliceux. Ensuite, mélanger jusqu'à obtenir une matière uniforme
- Appliquer le mastic mélangé en une seule passe à l'aide de la technologie de comblement de rayures. Consommation : environ 1,6 kg de mortier pour 1 m² et pour une couche de 1 mm d'épaisseur
- Ensuite, épandre immédiatement du sable siliceux fin avec une taille de grain de 0,2 à 1,0 mm sur le mastic tout juste appliqué.
Surface :
La surface doit être propre, sèche et exempte de substances pouvant nuire à la bonne adhérence. Les matériaux séparateurs ou couches, tels que les couches d'aggloméré, de poussière, d'huile, etc., doivent être éliminés à l'aide de mesures appropriées (décapage, fraisage, ponçage, aspiration et/ou dégraissage). La surface doit être suffisamment rigide pour les charges actives (se référer à la norme DIN 1055). Pour des chapes sur les couches séparatrices ou isolantes, il faut contrôler la maturité du revêtement avant d'appliquer le CERAfix 201. Le béton doit être conforme à la classe de résistance minimum C20/25 selon la norme DIN 1045. La chape doit au minimum appartenir à la classe C25-F4 conformément à la norme DIN EN 13813 et elle doit être en place depuis 28 jours. La teneur en humidité selon la méthode CM doit être inférieure à 4 CM% pour les surfaces à base de ciment. Pour les chapes en sulfate de calcium sans chauffage au sol, la teneur en humidité CM ne doit pas dépasser 0,5 CM% et pour les chapes en sulfate de calcium avec chauffage au sol, elle ne doit pas dépasser 0,3 CM%. Respecter les taux d'humidité résiduelle prescrits pour les revêtements suivants. Ce faisant, vérifier que la teneur en humidité résiduelle autorisée est respectée conformément aux préconisations de mise en œuvre. La mesure CM doit être effectuée conformément aux instructions de travail à jour "Coordination des interfaces pour les constructions de sols chauffés". Par la suite, éviter toute pénétration d'humidité. Lors de l'application et dans la semaine qui suit, les températures ambiante, du matériau et de la surface ne doivent pas dépasser +8 °C.
Choisir la couleur RAL
ATTENTION : Les couleurs que vous voyez à l'écran différent des couleurs réelles!